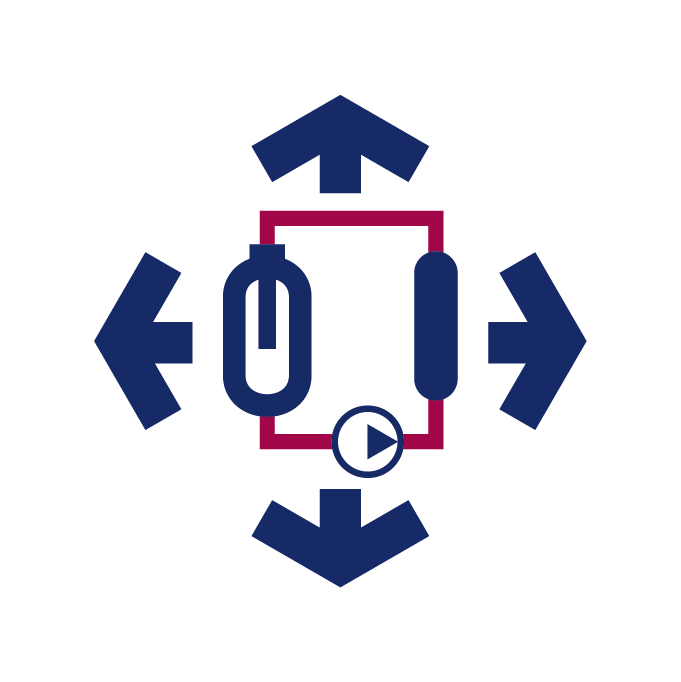
The initial development of a chemical reaction is often done in laboratory autoclaves, however kinetic effects should not be underestimated when it comes to the step from laboratory autoclave to industrial scale.
The results obtained in one of our laboratory- or pilot-scale BUSS-Loop® Reactors (1, 15, and 50 liters) can in the essence be linearly scaled up to any size of industrial reactor, due to the intrinsic system correlation to the energy input per unit of volume in the reaction mixer.
Scale-up factors up to order of magnitude of 1:103 and even 1:104 have been achieved, depending in the initial hypotheses and set of trials.
In the case traditional stirred reactors, scale up is difficult due to changes in flow patterns and area to volume ratios between a pilot plant scale and a production scale vessel. Mixing intensity cannot be scaled up so readily, as temperature and concentration gradients arise, often leading to longer reaction times and lower yields.
Advantages of the scale-up with BUSS ChemTech and the BUSS-Loop® reactors:
-
no changes in mixing patterns and area-to-volume ratios
-
linear scale-up in temperature and concentration gradients
-
independent adjustable scale-up of heat- and mass-transfer
-
virtually unlimited in reaction volume, due to no change in the flow pattern
-
more than 70 years in-house experience and database
Contact Us
* Required fields
Your Contact
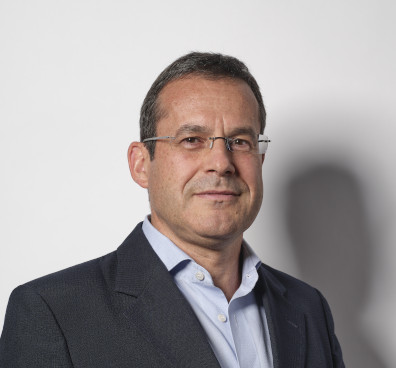
Gianluca Premoli
Business Manager Reaction Technology
Other Topics of Interest
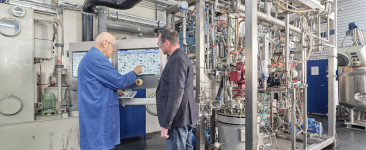
Determining Scale-up Parameters
Most often, tests to determine sizing parameters for an industrial scale plant are run in one of our several in-house pilot plants.
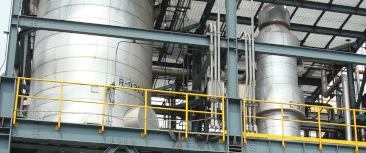
Tools & Techniques for Scaling-Up
At the core of our expertise, lies our know-how and experience of scaling up lab- and pilot-scale results into successful industrial-scale plants.
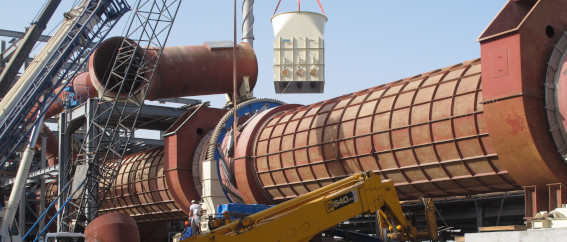
Scope of Project Delivery
From technology packages to modular and turnkey solutions, click below to find out about our range of services.